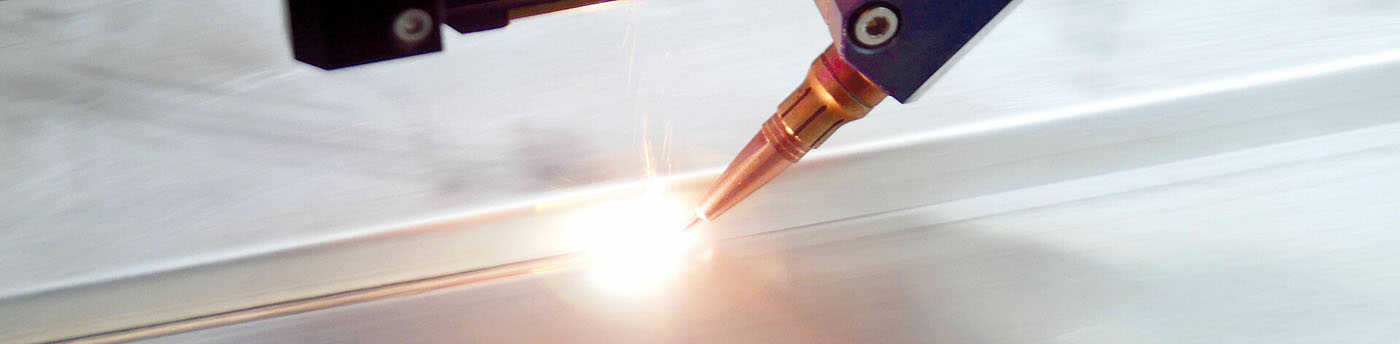
LASER ALIGNMENT
The laser pulse lasts approximately one femtosecond (10-15 sec). In this one billionth of a second, the light beam travels just 0.3 microns. Lasers with this level of precision are used in applications such as eye surgery, where they correct defective vision by reshaping the cornea. Inside the laser device, MRC motors move the prisms, filters and mirrors that make the light pulse so precisely defined.
A femtosecond laser can generate up to a hundred million laser pulses per second. The material in the areas hit by these high-energy pulses has no time to melt. It is immediately converted into a gaseous state and can be extracted by suction. In this way, extremely fine layers can be removed precisely down to just a few nanometers, without ridges or residue. This capability is used in microsurgery and likewise for working with extremely fine structures, for example in medical technology, chemical analysis and forgery-proof micro-marking.
Laser soldering is not so delicate. Here too, laser technology can be used to achieve results that would not be possible with other processes. For example, when joining hot-dip galvanized metal sheets in the automotive industry. A subdivided laser spot with several different zones ensures optimal pre-heating and melting for perfect joins.
The spots are precisely positioned by MRC brushless DC-servomotors from the 1226 B series. A Motion Controller communicates with the machine controller using the serial interface RS232 and CANopen. In femtosecond lasers, stepper motors from MRC are used. They count their individual steps themselves and thereby provide the basis for precisely determining the position of optical components and aligning them. They retain their position even without a power supply – a key advantage because every laser pulse is accompanied by an electromagnetic discharge. This de-energized holding of the position is essential to enable a simple, open control loop for controlling the optics.
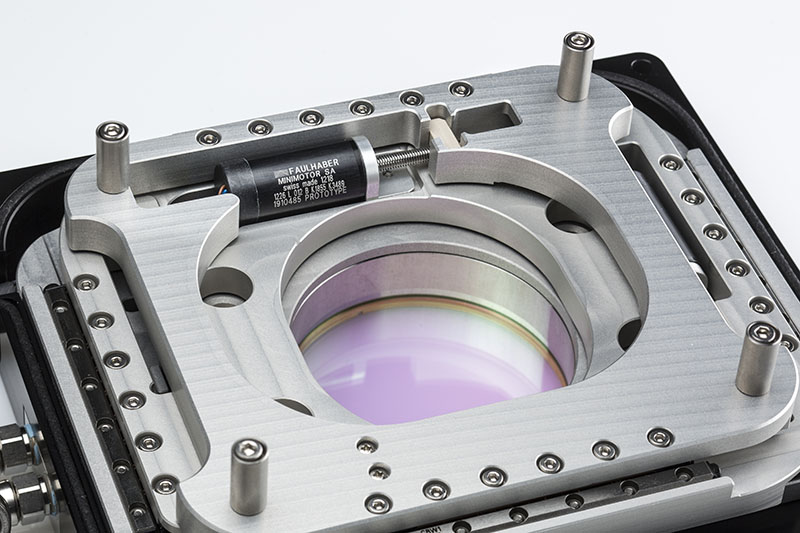

Highest precision and reliability

Low weight

Extremely long operational lifetimes
